How Overstock Inventory is Damaging Your Cash Flow
When you’re running a warehouse, you know that keeping the right inventory items on hand is a top priority. You need to keep fulfillment rates high to ensure customer satisfaction and to avoid inventory stock-outs.
However, stock-outs aren’t your only problem. Often, businesses experience financial challenges—and a lot of stress—over carrying excess stock.
Excess, unsold and unsalable stock ties up cash and storage space. It also erodes your bottom line in multiple ways.
What’s the harm in excess stock?
1. It’s costly to the bottom line and cash flow
The costs associated with inventory overstock tie up working capital that could be used elsewhere in the company. For example, it can force you to rent additional storage space.
Other costs associated with overstock inventory include:
- Insurance costs
- Extra labor and security costs for your warehouse
- Loss via obsolescence
- Loss via deterioration, breakage or expiration
- Loss due to write off or steep discounting
- Opportunity cost when your cash is tied up in overstock
We want to emphasize that last point about opportunity cost. The carrying costs for these additional items tie up money that you could be investing more wisely into business growth opportunities. You could be bringing on new product lines, updating your technology, or starting marketing campaigns to support market share expansion and growth initiatives.
2. It delays quality assurance time
Excess inventory drains your warehouse staff’s time away from performing quality inspections. It also gives them less time to properly maintain crucial inventory items.
When quality issues go undetected, vendors might continue to ship products with defects. In turn, you might supply defective products to your customers or use faulty items in your manufacturing processes. This puts your company and reputation at risk.
You can prevent quality issues by minimizing excess stock of materials that have a shorter shelf life so that you can sell or use them quickly.
3. It increases operating, labor and storage costs
Think about all the additional work that overstock creates. You have to pack, store, monitor, and handle every piece of excess inventory. As a direct result, you’ll have higher operating, labor and storage costs.
With all these added expenses, you’re less flexible to respond to market changes and customer demand. If your funds are tied up in excess stock, you won’t have the funds to purchase a product that could sell faster.
You should also be concerned about storage capacity and the related storage fees needed for overstock inventory. It takes space and resources to hold and manage inventory. You lose profits when paying rent for this additional storage space, and when paying labor to maintain the storage space, organize the stock and transport the stock from one place to another.
At the end of the day, keeping inventory lean has a positive impact on your cash flow and bottom line.
How to prevent overstock inventory
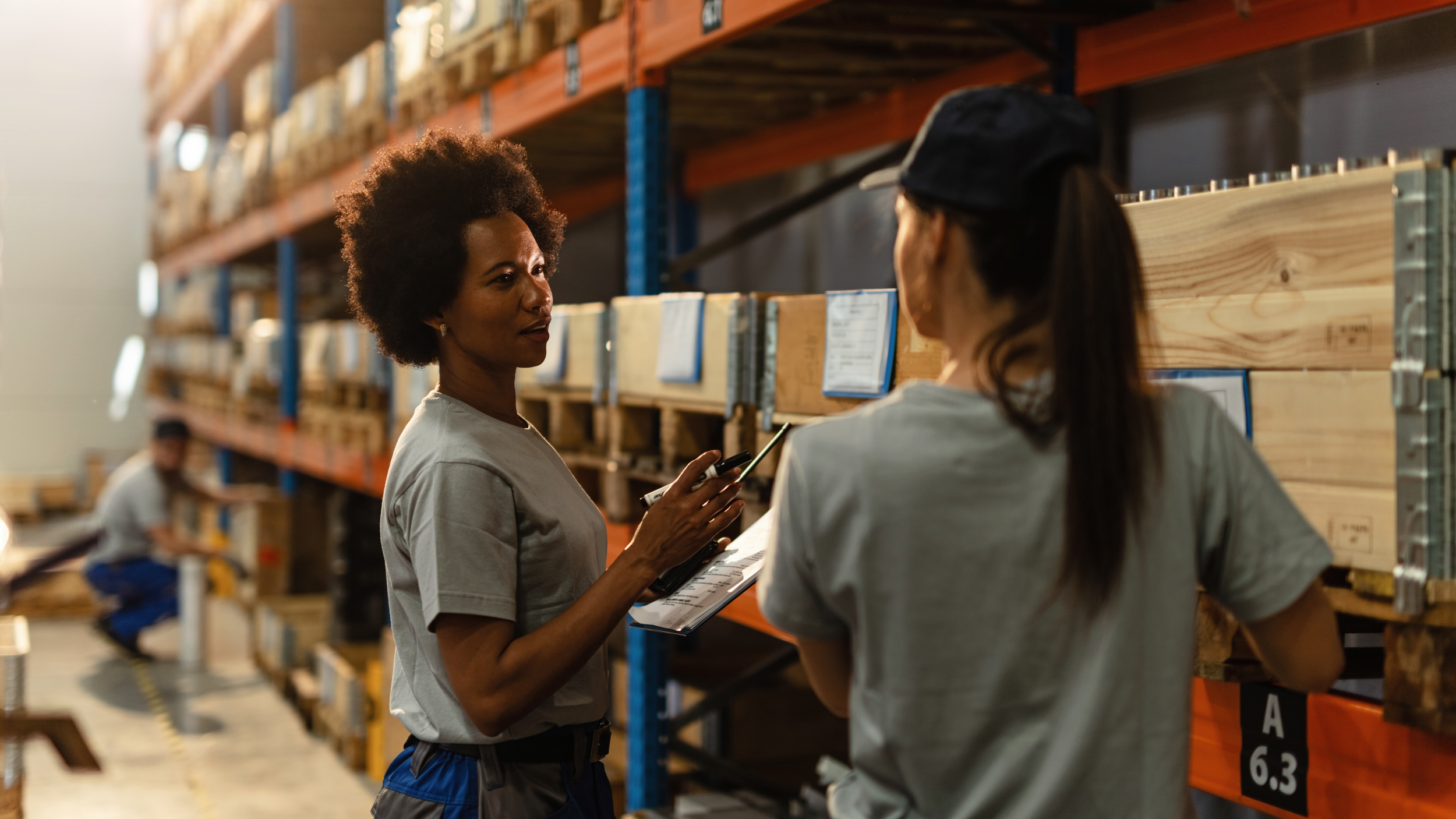
Create a safety stock policy
Profitable warehouses are built on a well-constructed safety stock policy. Instead of piling up on items that drain your funds, have a predetermined quantity of safety stock.
This excess—but planned—amount of product acts as a buffer in case sales are higher than expected or if suppliers fail to deliver on time.
What makes safety stock “safe”? For one, it’s a predictable quantity that minimizes the risk of unwanted overstock that might crowd your valuable warehouse space.
With a smart safety stock policy, you’ll optimize your warehouse space and free cash flow.
Abandon your outdated inventory tools
Are you still using inventory spreadsheets? They might be sufficient for uncomplicated businesses. But if you’re dealing with a complex and dynamic supply chain, you should upgrade to tools that match your company’s caliber.
These tools will help you manage the balance between safety stock and excess stock.
Inventory spreadsheets can’t effectively help you identify excess stock. They don’t give you a way to implement a dynamic safety stock policy that establishes the correct stock levels for every item. They don’t give you the visibility you need to have a profound understanding of your warehouse operations.
By sticking with your old inventory management tools, you’ll be managing a more expensive warehouse.
Get smarter tools
A dynamic enterprise resource planning (ERP) system can give you the insights you need—namely, keeping you on track for effective and efficient stock levels and preventing overstock situations. Consider a better inventory management system to give you deeper insight into your inventory needs.
A dynamic warehouse management system (WMS) will increase efficiencies, productivity and effectiveness of your warehouse activities. Providing a fully mapped warehouse, combined with paperless processing, will help you pinpoint precise inventory counts, placement, movement and picking. This, in turn, will improve customer satisfaction.
Consider a warehouse management system to optimize your warehouse and inventory flow.
If you want a supply chain that maximizes efficiency, productivity and profitability, there’s no such thing as a one-size-fits-all solution. That’s why you should consider investing in a customizable inventory management solution that isn’t just software—but a robust service that understands your specific needs.
Talk to us if you’re ready to optimize inventory levels and procedures while delivering end-user efficiency and productivity.